It should be remembered that the data posted in this report is from the first two years of a long term study. To this point the systems are performing very well. The infill systems are softer, less abrasive, and generally exhibit better traction qualities than traditional Astroturf. They maintained these qualities after 180 plus games of simulated traffic. The Gmax and traction values obtained from the synthetic surfaces are very comparable and in some cases more desirable than those measured on a similarly worn natural turfgrass area.
A review of current literature regarding safety and playability of infill synthetic turf systems can be found in the Athlete Performance and Safety section of this website. For the results of a survey of microbial populations in synthetic turf, please refer to A Survey of Microbial Populations in Infilled Synthetic Turf Fields found on this site.
Some things to consider when budgeting for an infilled synthetic turf system.
- Poor surface grading and lack of internal drainage are the two main construction problems encountered in infill synthetic turf systems in the USA. Currently, there are no standard specifications for drainage gravel installed beneath the backing of an infill system. The lack of an agreed upon standard has resulted in numerous installations with poor quality gravel that is either hard to grade to desired tolerances or that allows little internal drainage after compaction. The Synthetic Turf Council was formed in 2002 in order to produce a set of minimum specifications that will protect consumers from installations of poor quality synthetic turf infill systems (Synthetic Turf Council Inc., 2003). Currently, the council specifies that the sub-base drainage gravel of a synthetic turf field should provide adequate drainage and stability; however, a gravel particle size distribution is not specified. Subcommittees within the Synthetic Turf Council and in the F.08 division of ASTM are currently working on sub-base gravel specifications. The following link is to a set of specifications that have worked well. Gravel Drainage Specifications . By no means does this suggest that other drainage aggregates that do not meet this specification will cause drainage failure. They are listed here only as a guide. University and private labs can test drainage material to make sure they have sufficient permeability after compaction. After suitable materials are located, a quality control program during shipping is strongly suggested. The specifications provided are based on the specifications for drainage beneath a USGA golf green. These specifications can be found at: http://www.usga.org/turf/articles/construction/greens/recommendations.html . These specifications suggest quality control testing of the gravel every 500 tons.
- For heavily used fields, such as a high school where there is at least one sporting event per day, you should plan to broom the field weekly. This is done to keep the pile somewhat upright. This is different from grooming where the granules are loosened. Brooming can be accomplished by dragging a set of tennis court brooms or a piece of traditional Astroturf turned upside down across the field in varying directions. To reduce abrasion due to brooming, drag the tennis court brooms or Astroturf when the field is wet. Do not use a power broom weekly as this aggressive brooming will increase wear to the pile fiber due to abrasion.
- Grooming or loosening of the infill granules should be done at least once or twice per year. See the section on simulated foot traffic and grooming for details. Most field managers that we've talked to do not like the spring tine method of loosening infill because they feel it is too aggressive. Most like the star shaped unpowered slicer that we used (Fig. 32) and suggest a similar but larger model for field use. (Fig.33) See simulated foot traffic and grooming for details. Currently we suggest loosening the granules twice per year.
- The fields do get hot on sunny days. Some organizations have installed irrigation systems to reduce the heat. These fields warm up fast on clear sunny days but also cool down rapidly when the sun is not shining; there doesn't seem to be much of a heat sink. Irrigation of these fields dramatically reduce the surface temperature; however, in our limited testing we have found that a dramatic reduction in temperature is short term. Irrigation resulted in an average 15 degree F decrease in surface temperature for 200 minutes in our conditions. While irrigation may have a dramatic affect on surface temperature for a limited time and a limited effect over a longer time, it may prove beneficial in other respects such as washing in fabric softeners and wetting agents. Irrigation would also be beneficial in wetting the surface prior to brooming to reduce abrasive wear on the pile fibers. While these surfaces are hotter than natural turfgrass, the temperatures measured in this study of non-irrigated surfaces do not exceed traditional synthetic turf (Astroturf) that has been in use since the 1960s.
- There is a static build up on these surfaces, at least in year one when the fields are new. The only problem that I see with the static is aesthetic. The black granules tend to stick to the upright pile fibers and the field will temporarily look darker in high wear areas. The application of very dilute fabric softener will reduce this problem and has become a standard practice for some field managers. We have no data on the use of fabric softeners and their effect on playability. Some field managers have expressed their opinion that if fabric softener is used, it should be sprayed several days prior to an event as the material can make the field slippery if applied just prior to a game. Static tends to be a problem only with new systems. As the systems age the static is reduced; however, a new problem can arise--hydrophobicity. The granulated infill media in many systems can become hydrophobic. Precipitation will 'beadup' and roll off the surface rather than penetrate. An application of a wetting agent or surfactant may be required to maintain permeability over time. The effectiveness of wetting agents for this application has not been tested but in theory they should reduce the hydrophobicity of the infill media.
- The long-term durability of these fields is unknown. The duration of the warranties offered by synthetic turf companies has been set by economic and competitive issues as opposed to knowledge of the long-term durability of the systems. Originally, the standard warranty of a crumb rubber infill synthetic turf system was five years. Competition increased the warranty to eight years and for several projects the systems were warranted for 10 years. Currently, an eight-year warranty is considered standard in the United States. This author has seen some outdoor high-use fields that may last well beyond the warranty period while others look worn after only one year of use. Since the pile fibers breakdown due to both foot traffic and photodegradation, indoor fields will typically outlast fields that are exposed to sunlight. The author has observed thinning pile fiber in high wear areas around the goal mouth of high school lacrosse fields after only two years of use. There is no standard method to evaluate wear or thinning of the pile fiber. A warranty providing a guarantee against 'excessive wear' is open to interpretation.
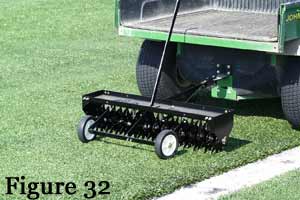
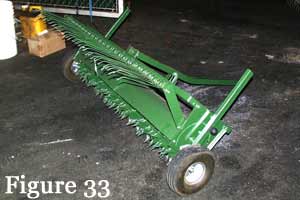
The Synthetic Turf Council (Daulton, GA) is a non-profit organization formed to set minimum quality standards for synthetic turf manufacturing and use in the United States. The council is currently wrestling with the issue of warranty duration and is considering suggesting some guidelines on system warranties (Synthetic Turf Council, Inc., 2003). Of critical importance to the consumer when trying to select an infill system is to consider whether that company will still be in business throughout the duration of the warranty. Some of the companies representing an infill synthetic turf system have already gone out of business in the United States. Of considerable note was the closure of SRI, Inc., owner and manufacturer of AstroTurf, AstroPlay, and NeXturf. From the 1970's through much of the 1990's this company was the largest manufacturer and installer of synthetic turf systems in the United States.
In the bid contract:
- Demand that the surface company pay for independent Gmax testing yearly for the length of warranty.
- Negotiate a maximum acceptable Gmax level lower than 200 (175 suggested)
- Demand good quality grooming equipment be provided.
- You'll also need a utility cart to pull the grooming equipment.
In conclusion we've made progress establishing testing methods for evaluation of these surfaces. This will allow us to more collect data more rapidly in the coming years. The infill systems generally outperformed traditional Astroturf in playing quality. The playing quality of these systems remained high after rather intense simulated traffic was applied. The playing quality of the infilled systems increased after brooming and grooming.